Several weeks before my resignation, I had been spending time online, reflecting on my career. One thing about working in semiconductors, or at least as a process engineer, is that you rarely feel ownership over the things you’ve done.
Any project you complete as you progress in your role often doesn’t lead to anything lasting. And when you reflect on what you’ve done so far, it’s hard to point to something that truly feels like your own.
Take the soft-bake process, for example: if you determine that temperature X is optimal for product Y on machine Z, chances are the result will change if you alter one of those variables, or anything dependent on them.
In practice, you don’t need deep process wisdom to succeed. What you really need is massive amounts of data, which requires a robust data collection system (as I mentioned in my previous post), and the ability to interpolate.
It is a great industry for people with data science or AI background, but not always the best fit for someone with a traditional engineering background. At least that's how I feel.
Anyway, I found and applied for a course called Siemens PLC Training with Manufacturing Industry
, funded by YP (Yayasan Peneraju) and organized by Pahang Skills (Pahang Skills Development Centre). It was actually designed as an upskilling program for fresh graduates. But since they didn’t receive enough applicants to meet their target, they reached out to me directly about joining. The time between being contacted and starting the program was less than a month (which explains the short-notice resignation).
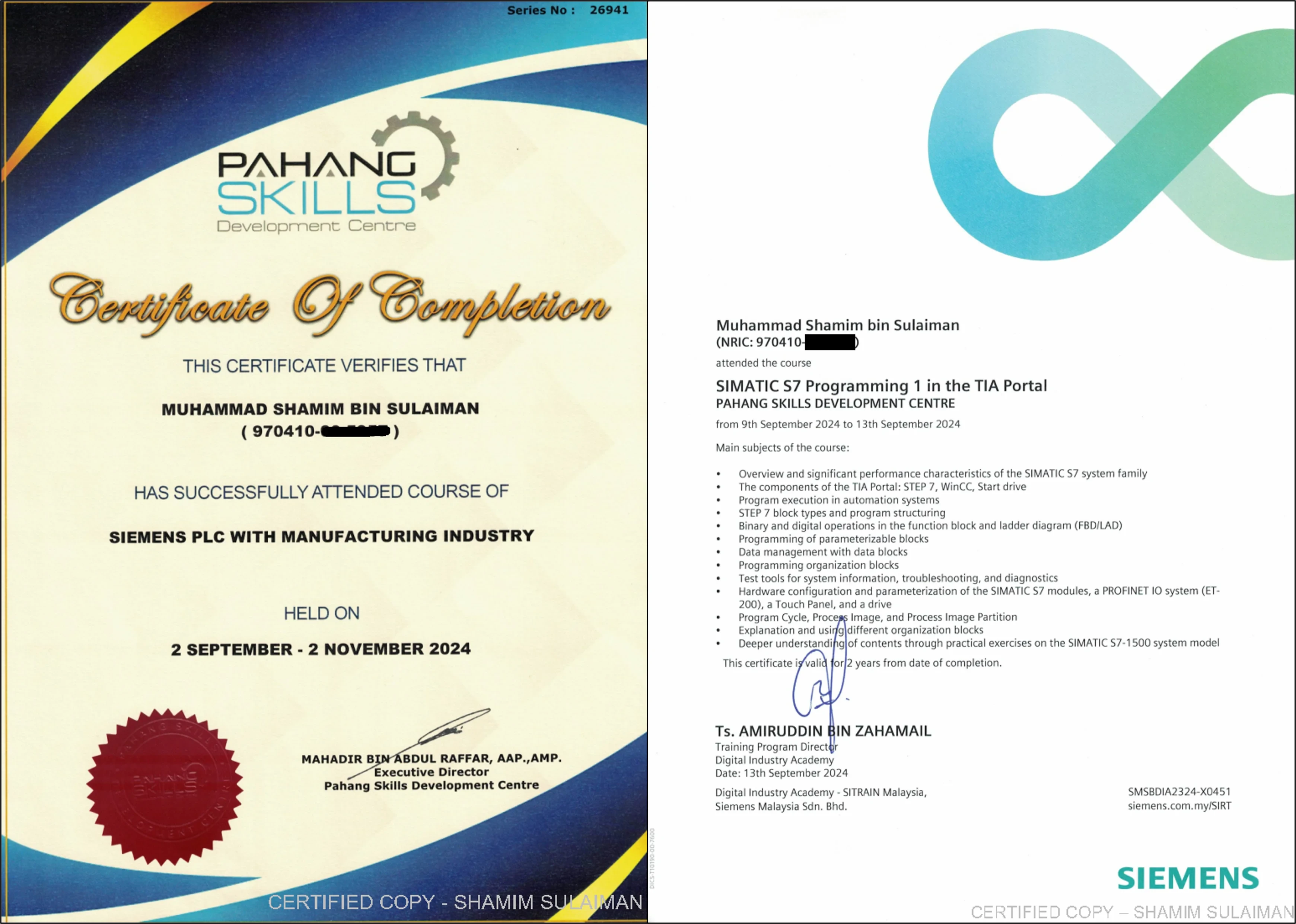
Why PLC?
When I first thought about PLCs, it felt like they existed in a sort of limbo, something every engineer had heard of, but few really understood well. Sure, I know the what PLC is and understood its importance for automation. But still I did some research online, read a few forums, and the more I looked, the more curious I became. On Reddit, some people even advised against pursuing PLCs as a career, most of them even called it a dark art.
Well, if you had asked me 8 years ago why I chose chemical engineering for my degree, I would’ve said:
"Because I wanted to know what it was all about."
So what do you think my answer is now?
Getting started
In this course, I didn’t just learn PLC, I also ended up learning a few other things that turned out to be crucial for me, given my background in chemical engineering. I lacked (or needed to refresh) the fundamentals of the electrical systems and their components, which I managed to learn. See the image below for the course modules I was exposed to.
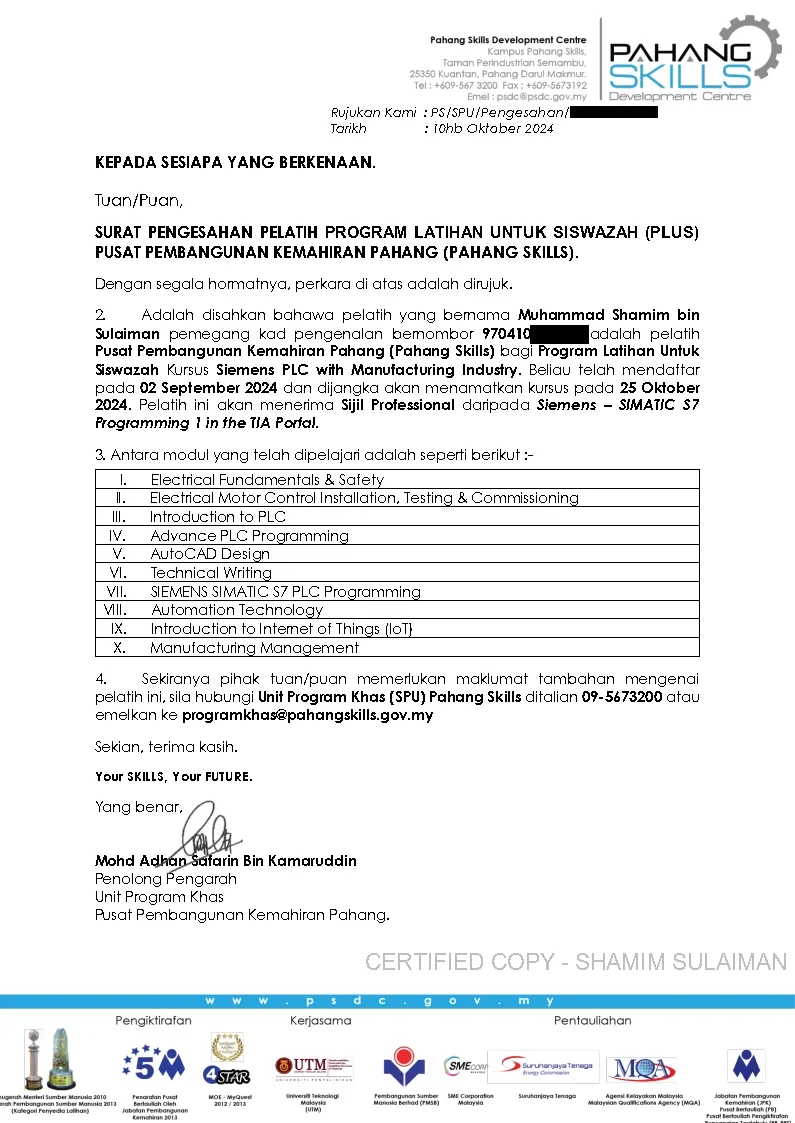
This course was quite intense, especially for someone without an electrical background. So instead of going into every single topic, I may just cover the modules that stood out the most to me. I learned a lot in a short amount of time. The most fun modules were:
- Electrical motor control system
- Electro-pneumatic system
- PLC programming (Siemens TIA Portal)
- IoT programming (Node-Red)
Electrical motor control system
In this module, we were introduced to:
- The fundamentals of electricity and the components used in control systems
- The difference between control circuits and main circuits
- The types of motors and how they work
- Wiring control systems using best practices and making sure nothing explodes
It was a good mix of theory and hands-on learning. At the end of the module (which consists of a few days), we were instructed to draw an electrical diagram for a motor control system, then physically wire it from scratch. This module was especially helpful for me, given my non-electrical background.
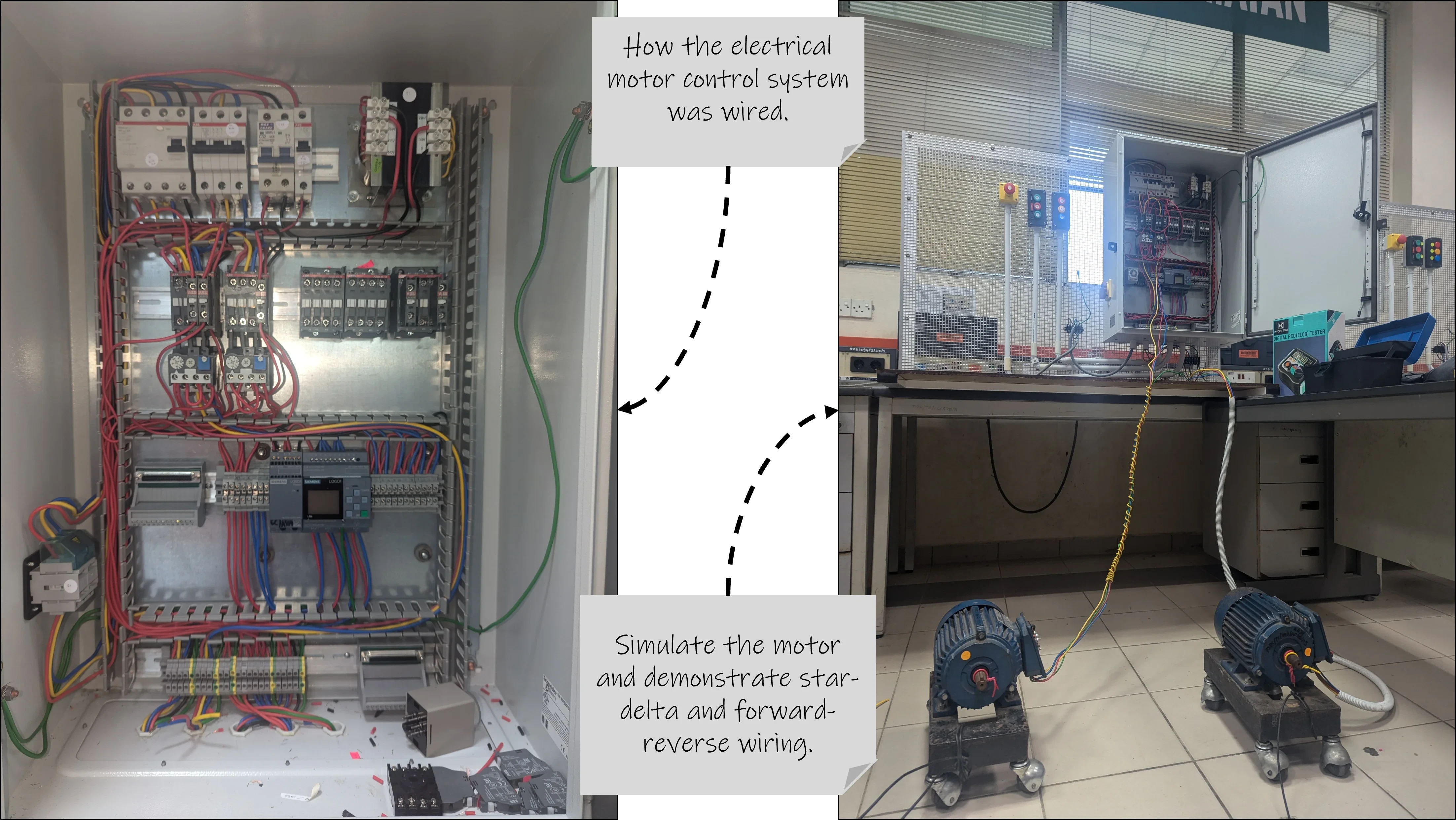
Electro-pneumatic system
This module followed a similar structure to the previous one, however the emphasized is on the pneumatic components. We covered:
- The fundamentals of pneumatic systems and their components
- Designing electro-pneumatic systems using Festo FluidSim
- Creating automation flowcharts using Grafcet
- Wiring sensors, actuators, and pneumatic cylinders into an electrical control system
Again, it was a blend of theory and hands-on practice. At the end, we were given a set of questions with each describing a desired control behavior. We had to create Grafcet diagrams, simulate them in FluidSim, and then implement the final solution using actual pneumatic components and electrical wiring. It was a satisfying process when everything worked as expected.
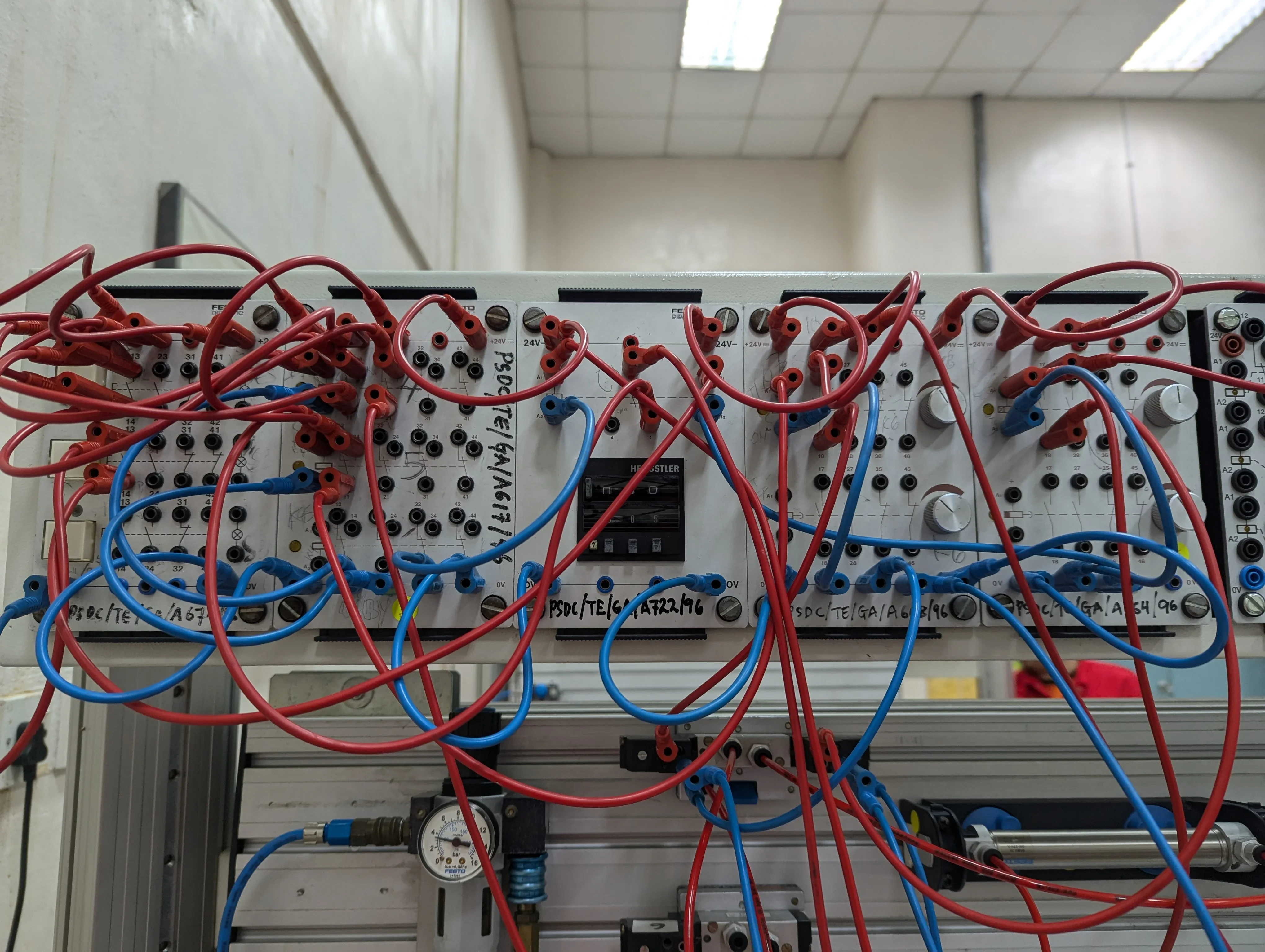
I’ll continue sharing the rest of the modules and what I learned in the next post (maybe).