Siemens PLC Training
Projects | | Links:
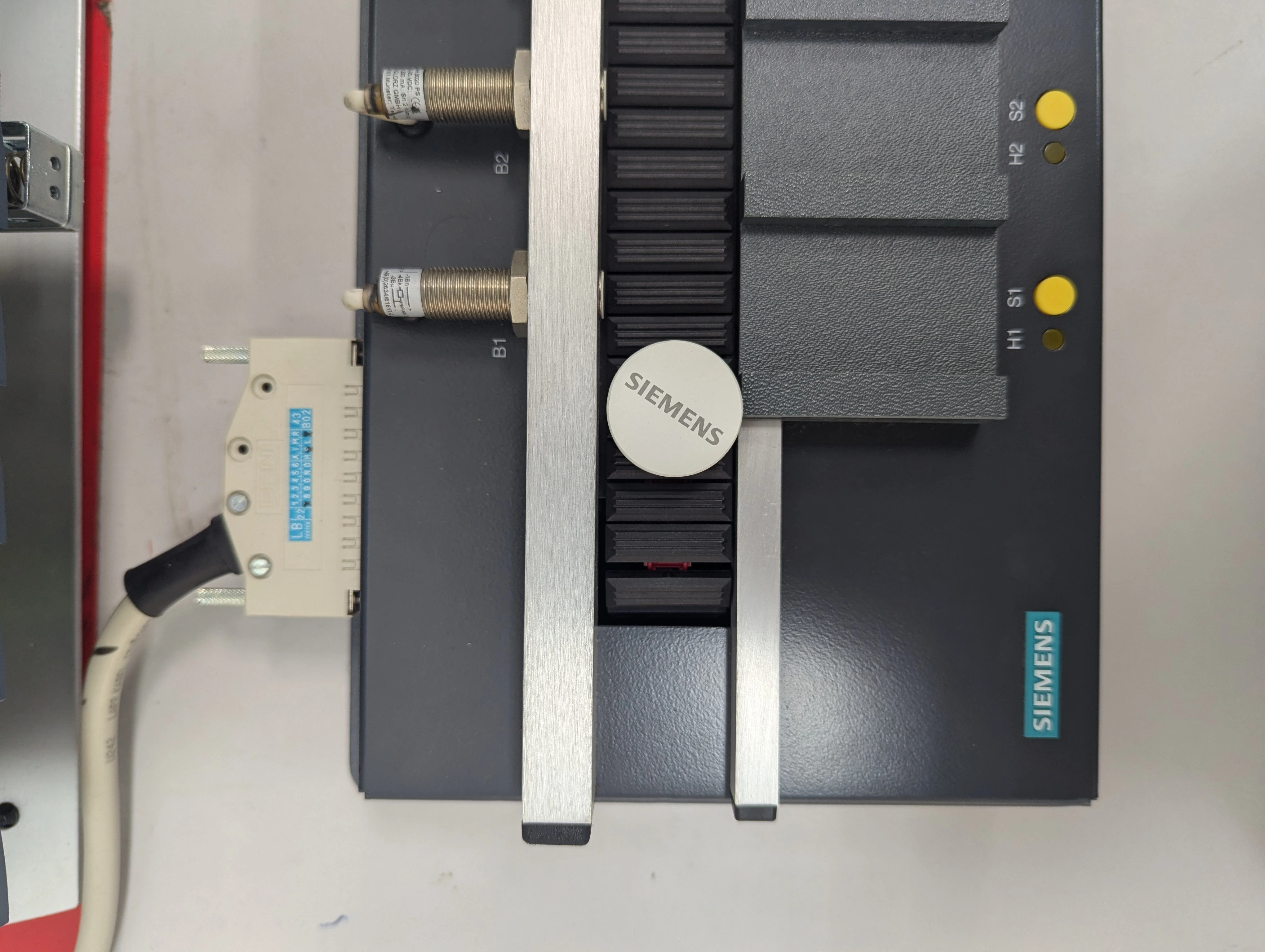
2-months Siemens PLC training at Pahang Skills.
In September 2024, shortly after I left UAT, I joined the Siemens PLC Training at Pahang Skills Development Centre. The reason? To learn automation.
I realized how important automation is when I was a Process Engineer at you-know-where,—and also how badly it was lacking there. Every new machine was locked behind complicated SECS/GEMS protocols, the RMS system was limited, and the old machines were just patched up with standalone PLCs. Good systems on their own, but together? A total mess. No synergy, no proper integration. If they had revamped the entire system properly, one process engineer could probably handle everything instead of five. But hey, just my opinion (not that it matters).
Even though this PLC course didn’t include SECS/GEMS, it’s still a solid start. PLC is everywhere in manufacturing, and learning it felt like the first step into real industrial automation. The main things I picked up from this training:
Electrical Motor Control System
We started off with motor control systems—because what’s automation without motors, right? It was a mix of theory and hands-on practice. We covered:
- Electrical components used in motor control.
- The difference between control circuits and main circuits.
- Different types of motors and how they work.
- Wiring up the control system and making sure nothing explodes (just kidding… or am I?).
The control and main circuit done for forward reverse motor.
Forward reverse motor simulation. One of us messed up the looping, and his contactor turned into an AK-47. Good times…
The hands-on part was cool. We wired up motor control panels, checked connections, and ran tests (continuity, polarity). Seeing it all work after setting it up? Very satisfying.
Electro-Pneumatic System
Next up—electro-pneumatics. This was where things started to feel more automation-like. Pneumatics is all about air-powered systems combined with electrical control, and we got to:
- Design the system using Festo FluidSim.
- Create Grafcet diagrams (basically automation flowcharts).
- Wire up sensors, actuators, and pneumatic cylinders.
It was fun getting hands-on with different sensors and actuators, seeing how they interact, and actually making a pneumatic system do what I wanted it to do.
Another electro-pneumatic circuit done by me. Not bad for a chemical graduate huh…
NSFW.
There’s still more to share, but I’ll save the best for later.